Professional Advice on What is Porosity in Welding and Just How to Address It
Professional Advice on What is Porosity in Welding and Just How to Address It
Blog Article
The Scientific Research Behind Porosity: A Comprehensive Overview for Welders and Fabricators
Recognizing the elaborate systems behind porosity in welding is crucial for welders and producers making every effort for impeccable workmanship. From the structure of the base products to the ins and outs of the welding process itself, a wide range of variables conspire to either aggravate or ease the presence of porosity.
Understanding Porosity in Welding
FIRST SENTENCE:
Assessment of porosity in welding exposes vital understandings into the integrity and quality of the weld joint. Porosity, defined by the existence of dental caries or voids within the weld steel, is an usual problem in welding procedures. These gaps, if not properly resolved, can compromise the architectural stability and mechanical properties of the weld, causing prospective failures in the finished item.

To discover and evaluate porosity, non-destructive testing approaches such as ultrasonic screening or X-ray inspection are typically used. These strategies enable for the recognition of inner defects without compromising the integrity of the weld. By assessing the dimension, form, and circulation of porosity within a weld, welders can make educated choices to boost their welding procedures and achieve sounder weld joints.
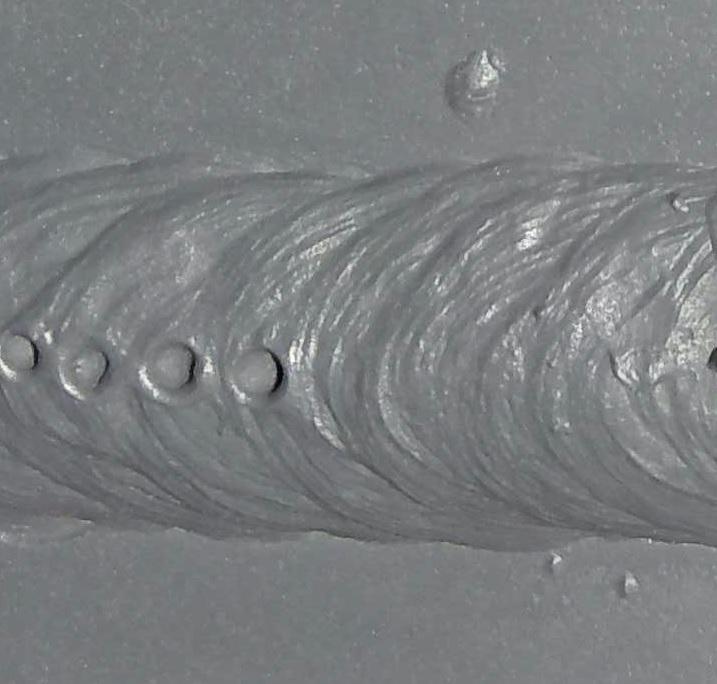
Aspects Influencing Porosity Development
The event of porosity in welding is influenced by a myriad of elements, varying from gas securing efficiency to the details of welding criterion settings. Welding specifications, consisting of voltage, current, travel rate, and electrode kind, additionally impact porosity formation. The welding method utilized, such as gas steel arc welding (GMAW) or secured metal arc welding (SMAW), can affect porosity development due to variations in warm circulation and gas coverage - What is Porosity.
Effects of Porosity on Weld High Quality
Porosity formation dramatically compromises the structural integrity and mechanical buildings of welded joints. When porosity exists in a weld, it develops spaces or dental caries within the material, minimizing the general strength of the joint. These gaps work as stress and anxiety concentration factors, making the weld more susceptible to breaking and failing under load. The presence of porosity also compromises the weld's resistance to corrosion, as the trapped air or gases within the voids can react with the surrounding atmosphere, bring about destruction over time. In addition, porosity can hinder the weld's capability to hold up against stress or influence, additional jeopardizing the overall quality and dependability of the bonded framework. In crucial applications such as aerospace, auto, or structural constructions, where security and toughness are vital, the damaging impacts of porosity on weld quality can have severe consequences, stressing the importance of decreasing porosity via appropriate welding methods and procedures.
Techniques to Decrease Porosity
Furthermore, making use of the proper welding specifications, such as the right browse around this site voltage, existing, and travel speed, is important in avoiding porosity. Preserving a consistent arc length and angle during welding also aids reduce the possibility of porosity.

Making use of the proper welding technique, such as back-stepping or utilizing a weaving motion, can also aid distribute heat equally and minimize the opportunities of porosity development. By carrying out these methods, welders can effectively decrease porosity and create top quality bonded joints.
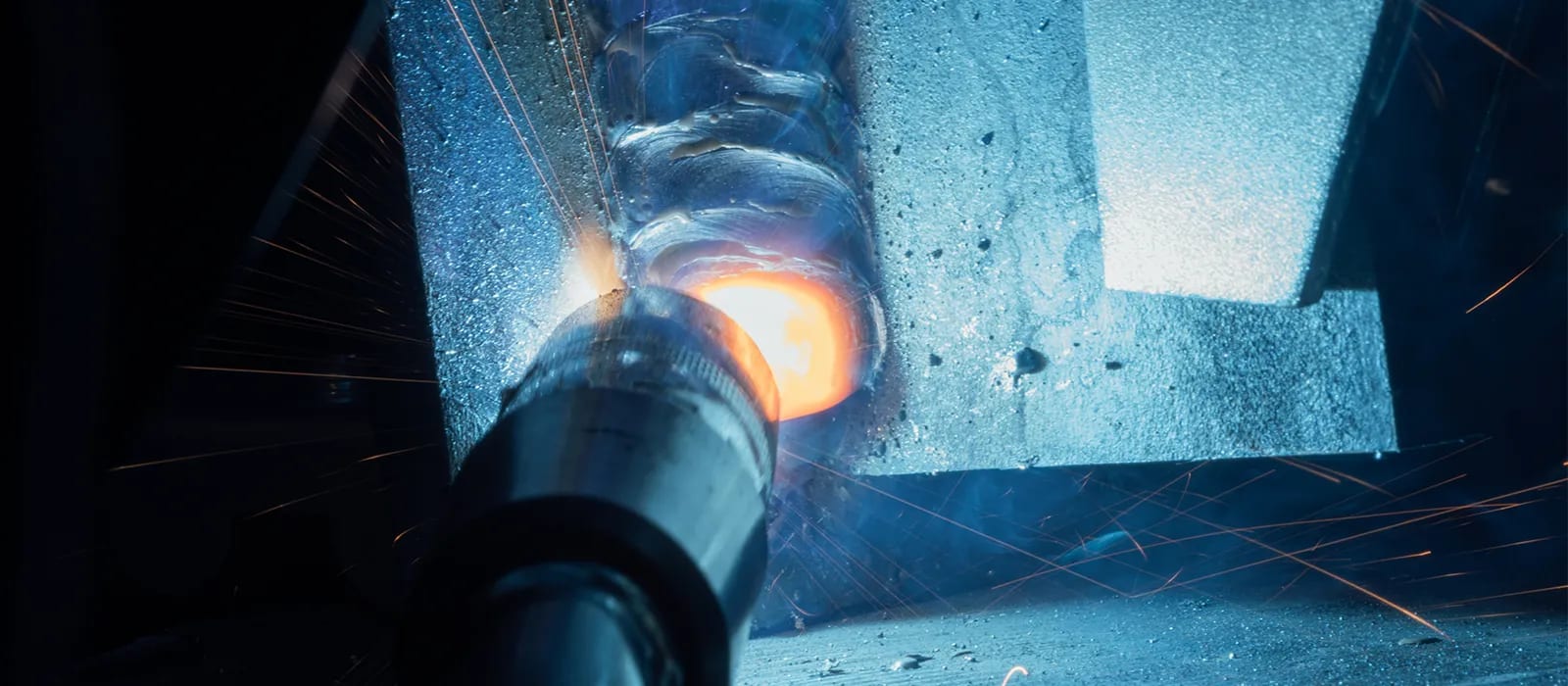
Advanced Solutions for Porosity Control
Applying advanced technologies and ingenious approaches plays a pivotal function in attaining superior control over porosity in welding procedures. In addition, employing sophisticated welding strategies such as pulsed MIG welding or modified environment welding can additionally help reduce porosity concerns.
Another advanced solution includes making use of innovative welding devices. As an example, utilizing tools with built-in functions like find more information waveform control and innovative power sources can improve weld high quality and lower porosity threats. Additionally, the application of automated welding systems with specific control over criteria can dramatically minimize porosity defects.
Additionally, incorporating advanced monitoring and assessment technologies such as real-time X-ray imaging or automated ultrasonic screening can assist in finding porosity early in image source the welding procedure, permitting immediate corrective activities. On the whole, incorporating these sophisticated options can considerably boost porosity control and improve the total high quality of bonded parts.
Final Thought
To conclude, understanding the scientific research behind porosity in welding is necessary for welders and producers to generate high-grade welds. By identifying the aspects influencing porosity development and applying techniques to lessen it, welders can boost the general weld high quality. Advanced services for porosity control can even more improve the welding process and make certain a solid and trustworthy weld. It is vital for welders to continually inform themselves on porosity and carry out ideal methods to accomplish optimal results.
Report this page